It’s Been a Year Since the Suez Canal: What’s Changed?
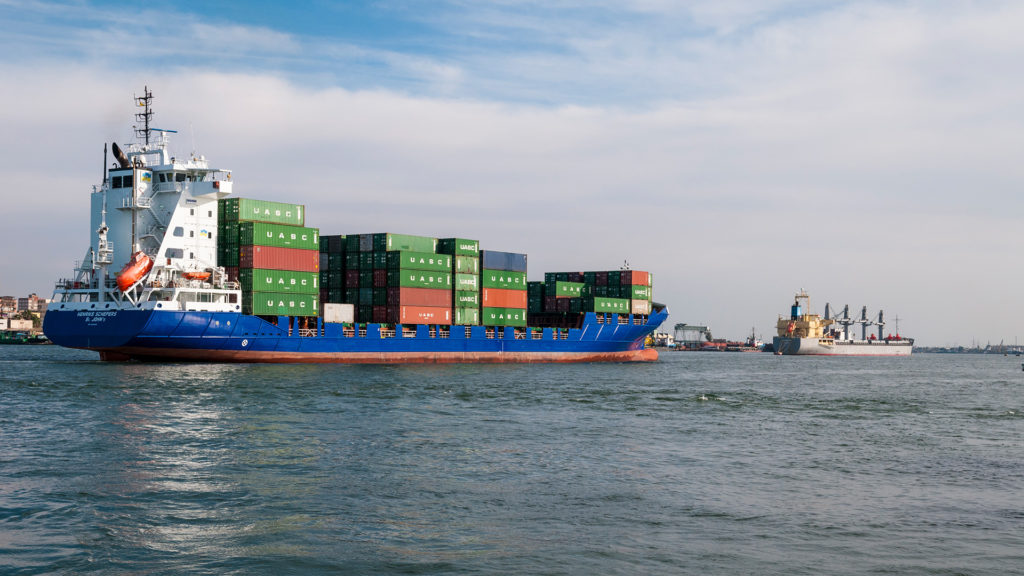
The effects of Suez Canal Blockage 2021 have been global in more ways than one. Over the course of 2021, there have been a number of disasters, both on land and at sea. While the world was finally shrugging off the impact of the first wave of COVID-19, another black swan event struck the global supply chain — the ripples of which create an impact to date.
On March 23rd, 2021, the Ever Given, a ship owned by the Japanese shipping company Shoei Kisen Kaisha Ltd., was caught in a sandstorm while traveling through the Suez Canal. The 46mph winds caused the ship’s hull to deviate from true, and the vessel ran aground and became lodged diagonally, effectively blocking the canal for just over six days and impacting global trade.
The fully loaded 20,000 TEU vessel was traveling from Tanjung Pelepas, a port in the Johor Bahru district of Malaysia, and was en route to Rotterdam in the Netherlands. The ship’s cargo included products for many name brand manufacturers including IKEA, Caterpillar, and Lenovo, as well as freight for a number of smaller businesses.
As we approach the one-year mark since the infamous Ever Given fiasco, we now look at the broader picture and overall impact of the incident.
Dissecting the Effects of Suez Canal Blockage 2021: Post-Incident
What was supposed to be a nine-day trip turned into a four-month ordeal for companies waiting to receive their freight. While this was an inconvenience for larger companies, the hold-up was near-disastrous for SMEs. With billions of dollars worth of products being held for months — not just on the Ever Given but also in the queued vessels stuck on both sides of the canal — the situation quickly turned dire.
Order Smaller Volumes More Often: Just-In-Time Inventory Management
There are two schools of thought that can help companies stay resilient and manage inventory better against such disruption. The first is to order smaller volumes more often, known as a Just-In-Time (JIT) inventory management practice. This allows businesses to keep pace with ever-changing consumer trends and tastes, and reduces the inventory volume needed to be stored, tracked, and managed at any given time. The advantage to smaller, continuous orders is that should the supply chain be disrupted, the company isn’t left waiting and can, instead, source their products elsewhere.
The drawback with running a leaner amount of inventory is that a sustained disruption, such as that caused by the combination of both the pandemic and the Suez Canal blockage can quickly wipe out any reserve stores of inventory.
Order Higher Volumes Less Frequently
The other school of thought is to order higher volumes less frequently. For standardized or timeless commodities that don’t run the risk of falling out of fashion, the advantage is decidedly less shipping costs. Additionally, ordering larger quantities and maintaining a higher volume of inventory can allow companies to hold out through a protracted disruption. However, when a supply chain disruption occurs during the order period, smaller companies may not be in a position to order more stock from a different supplier.
Have Inventory Management Best Practices Changed?
It is important to note that the year prior to the Suez Canal Blockage incident, supply chains were already being drastically strained by the global pandemic, one of the worst global supply chain disruptions the world has seen in recent memory. When the Ever Given grounded across the canal, it caused a backlog of somewhere between 300 to 400 ships waiting to pass. Every ship that was delayed caused a further delay somewhere downstream.
Those continuous delays will continue to ripple through the supply chain, adding strain until something inevitably has to give. In this case, the port congestion throughout the United States reached critical mass. US ports are struggling to process the sheer volume of ships and freight coming in from overseas. As a result, many companies are having issues keeping shelves stocked as ongoing shortages sweep through every industry.
This type of delay underpins the inherent weakness of the JIT philosophy. While keeping inventory low can reduce operating costs and improve overall cash flow, it is not able to adapt to disruptions that are significantly prolonged — like the case of COVID-19. JIT technique has issues with pivoting quick enough to compensate for sudden demand spikes, even when safety stock is taken into account.
Companies are Embracing Change
Companies are looking for means to pivot their operations around disruptions as high demand, container shortage, semi-conductor shortage, and port congestion problems affecting US ports are not going away anytime soon. This pushes companies to change the way they look at and manage inventory levels.
For starters, we can expect to see more manufacturers expanding their list of vendors and sources for raw materials and ready-made components to create a more diverse supply line. This creates more opportunities to source materials in the event of disruption like the Suez Canal blockage. For larger companies, this will extend to onshoring and offshoring manufacturing, as it reduces the dependency on any single geographical location.
While lean manufacturing has been touted as “the way it should be done,” many organizations will be embracing less stringent policies when it comes to the amount of on-hand inventory and inventory turnover levels in favor of maintaining a sustainable supply/demand ratio regardless of the present scenario.
Most importantly, we will see more companies beginning to take a greater degree of control over their supply chain through digital supply chain management and greater utilization of third-party logistics provider (3PL) services. While the push for digitization of the supply chain has been ongoing over the past few years, the need has become decidedly more pressing. The domino effect of global supply chain disruptions has served as the tipping point for many companies that were on the fence about going digital or seeking help through a third-party service provider.
To answer the question — yes, inventory practices have changed. Not only have they changed, but they will continue to do so with time. We are in the midst of a supply chain renaissance as we have seen just how vulnerable the global supply chain truly is today. While we are a long way away from reaching pre-pandemic normalcy, we might be on the right track. Plan ahead and register with ShipWorks to streamline your shipment process!