Tackling Common Warehouse Shipping Issues
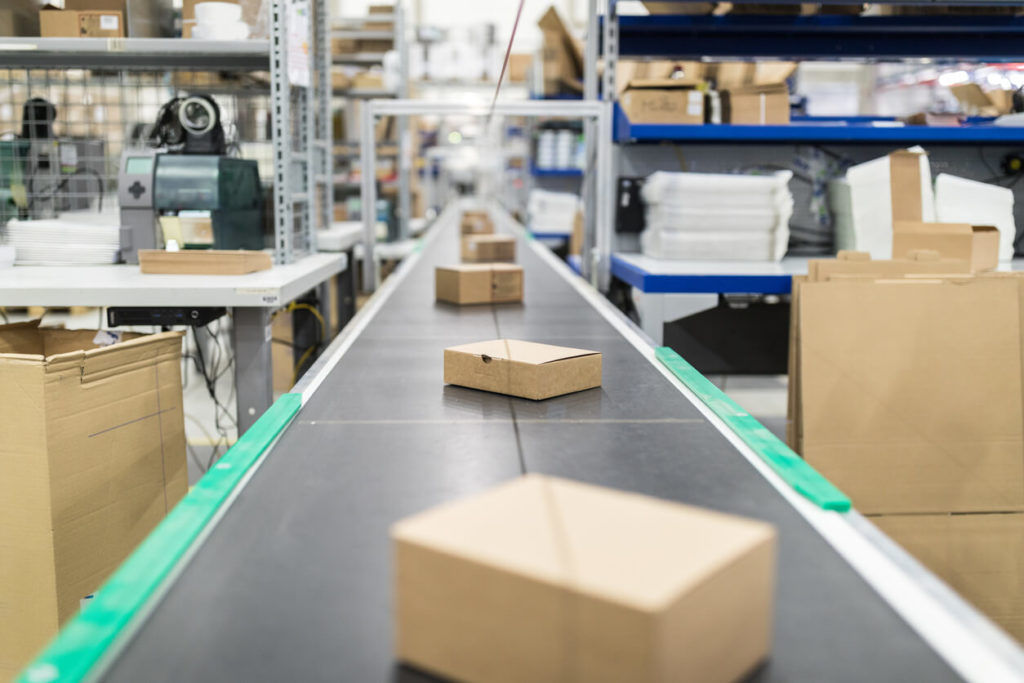
For business owners, selling generally revolves around convincing their target audience of product quality and customer support. For customers, buying can be delightful only if the product reaches them on time and without damage.
In sales or purchases that happen online or over long distances, warehouse shipping conditions and their handling of products are pivotal. So many things can go wrong in terms of logistics and warehouse shipping mistakes. However, they can be identified, addressed, or rectified easily.
What Are the Most Common Shipping Warehouse Mistakes?
Cost-related Problems
In today’s world, everything changes rapidly. Transportation costs are no exception. It is a mistake to assume that today’s costs are the same as that of yesterday.
In a bid to ship the fastest, shippers tend to pay exorbitant charges. The cost difference between next-day morning and afternoon deliveries can be considerable. Although faster, shipments by air are much costlier than ground delivery, especially to nearby places.
Shippers should research all possible shipping methods and costs. Some other best practices that can be adopted to reduce costs and avoid warehouse shipping mistakes are using vendor consolidation when shipping large volumes and ensuring proper packaging to counter damage.
Inventory Issues
Products being out of stock, lost, damaged or broken are signs of a disorganized inventory. Another example of warehouse shipping problems is shipping a wrong order.
Warehouses should have designated spaces for their inventories and maintain them with accuracy. They should double-check every item they send and be aware of the items that need replenishment.
Infrastructure Lacunae
The ideal warehouse should have the right amount of unobstructed space for easy material handling. Docks, loading bays, turnarounds and parking areas should be laid out, with due consideration to security, safety, efficiency, expenses, and future expansion.
Storage and Retrieval Inefficiencies
Around 50 percent of labor resources in warehouses involve picking, packing and shipping. Warehouses that have inefficient layouts, lack good equipment, and have disorganized storage may face issues, such as slow picking. This increases the likelihood of warehouse mistakes and shipping problems. They should employ personnel to clean messy loading docks and aisles and keep everything organized so that people and goods can pass through easily.
Just as important as dispatching orders carefully is receiving inbound goods. Warehouses should allot dedicated staff to check, receive and maintain them. Quality storage and material handling equipment are indispensable in ensuring the efficiency and safety of staff members.
Health and Safety Hazards
One of the major challenges warehouses face is ensuring the safety of their workforce. The warehousing industry has a higher-than-average fatality rate as the workers encounter several potential hazards, such as unsafe operation of equipment, electrical and fire mishaps, and more.
Warehouses should be assessed for safety. They should report accidents and near misses, analyze the causes, and eliminate them. They must foster a safety culture and ensure that the right safety equipment is used by all workers to prevent safety warehouse mistakes.
Employee Engagement Errors
Although employees are the greatest assets of warehouses, their training and development is often neglected because of insufficient budgets. This would lead to lack of motivation, increase in errors and warehouse mistakes, and eventually, attrition. Warehouses should monitor performance and train employees so that they are efficient enough to handle their jobs.
Automation Woes
Many warehouses still stick to traditional methods to solve any shipping problems. They fail to use technology such as warehouse shipping software and continue with inefficient workflows. Investing in technology like large warehousing providers will enhance their functionality and efficiency.
Conversely, technology may also pose problems if not handled well. Warehouses shouldn’t shy away from it; instead, they should check what is wrong and make corrections.
General Glitches
Lack of communication and research on issues that affect international shipping; awkward scheduling; incorrect documentation; and ignorance of commonly used metrics can also cause problems at warehouses.
A well-run warehouse shipping operation consists of excellent people, processes, and environment. If it manages them well, it can improve further and face any major warehouse shipping issue with ease.
Use ShipWorks warehouse shipping software free for 30 days to see for yourself how powerful we can be, yet how easy to implement. If you want to speak to our team about your specific requirements as well as see ShipWorks in action, please schedule a free demo or discovery call here and we’ll be happy to show you around!