What Is Warehouse Automation?
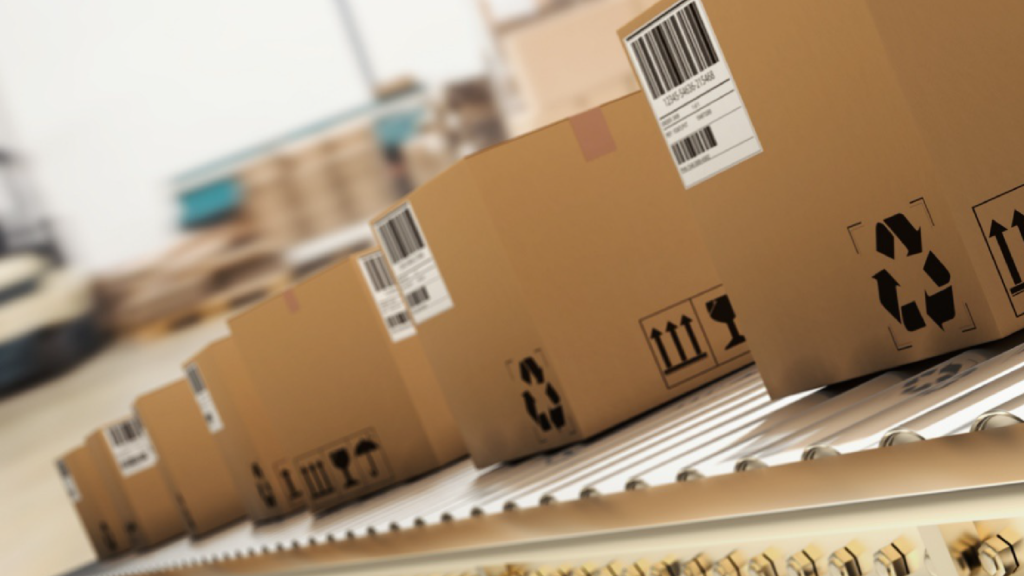
Warehouse automation involves moving inventory into, within, and out of warehouses with minimal assistance. The goal of automation is eliminating labor- and time-intensive tasks that involve physical work, manual data entry and analysis, or inventory accounting processes. Automation does not require replacing physical tasks or robotic replacements. In many cases, it refers to using software to replace mundane manual tasks.
When business owners look for options that can enable their business to scale, they first evaluate time recovery. When a task can take hours per day, such as label printing for Blue Sky Scrubs, every minute saved yields an appreciating ROI. Every minute saved gives the opportunity to save another. Businesses have successfully saved hours per day using a time-efficient warehouse management system (WMS). Imagine reclaiming two or three hours per day. Over the course of one working month, you’ll reclaim a full working week—per employee involved.
Warehouse automation generally involves replacing roles such as address verification, carrier data entry, and warehouse design—with respect to placing and rotating stock inside the warehouse. Each of these tasks require data entry and analysis as well as basic arithmetic operations such as solving optimization problems.
Signs of an Inefficient Warehouse System
No growth-oriented business should face inefficient warehouse operations and warehouse management in the modern age. Unlike poor-quality products and underperforming personnel, it’s difficult to identify warehouse inefficiencies in many cases—they’re not immediately noticeable.
Some symptoms that may signal warehouse inefficiency include ongoing or frequent order errors, payroll mismanagement, unnecessary stock counts and inventory miscounts, and inventory shrinkage. Businesses often see these symptoms when their resources are misaligned or overlapping.
If you experience one or more of the following problems, it might be time to evaluate your warehouse efficiency.
Ongoing Order Errors
Improper binning, mislabeling, and poor picking practices are just a few potential roots of ongoing order errors. These issues often result in customer returns and exchanges. When these problems persist, your brand reputation will suffer—poor reviews and declining sales numbers quarter over quarter may be KPIs that can signal recurring order errors if there aren’t enough returns to trigger internal action.
Payroll Mismanagement
Employees and contractors are the lifeblood of shipping and logistics. Without skilled personnel and clear standard operating procedures, systematic inefficiency will develop throughout entire enterprises. If overtime and other resource allocations are substantially over projected values, you may be contending with warehouse inefficiency.
Warehouse Cleanliness
In manufacturing environments, workspace cleanliness is easy to monitor. In warehouse environments, this may not be the case—particularly for workers who are executing stocking and stock rotation tasks. In some cases, parts, packages, and tools may be strewn about, with some barely exposed under warehouse shelves.
Worker’s compensation claims, poor inventory accuracy, declining productivity, and several other signs may allude to this risk factor. OSHA violations, which may arise as a result of an unclean working environment, are often costly atop the other expenses your business may face, such as insurance rate increases and employer match or other fiscal responsibilities.
According to Anthem (Blue Cross, Blue Shield), employers pay over 80% of employee healthcare premiums on average and around 70% of policy costs.
Inventory Shrinkage
Sometimes inventory begins disappearing from the warehouse. This can be a direct result of aging out (expiration, End-of-Life, etc.) or due to another factor entirely. It’s not impossible for warehouse workers or visitors to help themselves to your inventory, either. This commonly happens when inventory is poorly managed and excessive stock just sits in the warehouse.
There are few ways to ultimately track warehouse stock, however, so it is often difficult to know precisely why inventory is disappearing. You know that inventory shrinkage—whether due to theft, or otherwise, is a definite signal that your warehouse needs help.
Unnecessary Stock Counts
At first glance, you might imagine that unnecessary stock counts refer to calling for inventory too often, perhaps out of a lack of trust, or otherwise.
Unfortunately, the issue is often far more costly. Failure to maintain proper inventory can result in overstocking at best, and in some worse cases, a lack of space for high-demand inventory. Lacking floorspace is particularly devastating in times of demand shock.
For instance, the beginning of COVID was marked by a series of limited scope supply and demand shocks. One of the most commonly referenced from that period was consumer demand for toilet paper. In a very short period of time, people went from having consistent access to toilet paper to having a complete inability to purchase any toilet paper at all.
Because demand for toilet paper had never reached such levels in the past, warehouses were unable to match this spike in demand. Many stores lost out on their ability to sell toilet paper, which eliminated auxiliary sales opportunities that came with having customers in the store.
Wasted Time and Wasted Steps
Wasted time occurs due to a combination of factors that can be readily remedied. Some factors that influence wasted time include poor warehouse design, inefficient floor space allocation. and inefficient equipment. Saving a few minutes per employee adds up to a massive amount of lost potential profit, specifically when averaged across an entire warehouse of staff.
Mobile scanning, goods virtualization, and real-time 3D inventory controls are just a few technological solutions that empower businesses to overcome systemic inefficiencies that can cost tens of thousands of dollars per year. Average employees operate for roughly 2080 hours per year.
If a warehouse worker spends just one in ten hours walking to and from bins that should have been placed by the loading area, rather than four rows into the warehouse, they will spend over 200 hours per year on inefficiency that could have been resolved through simple shipping and receiving improvements.
Learn how your business can benefit from shipping and receiving improvements, such as warehouse automation.
The Benefits of Warehouse Automation
ShipWorks provides a complete suite of software for automating warehouse operations such as warehouse planning, label printing, and carrier data entry. Companies are able to carry out more accurate warehouse planning operations using warehouse management software (WMS), such as the ShipWorks suite.
Combined with RFID or NFC tracking beacons, ShipWorks WMS is able to efficiently monitor stock movements. Some such interactions may come in the form of log data, for example:
———
Log Report (Page 125, 821 of 125,897) for July 4th, 2020
———
Log Date – July 4th, 2020, 22:31:46
[PALLET 00023 19243 23] (UPC Identification number) was COLLECTED from [BIN 31 11 3]
by [LIFT 12] under Operator ID [Doe, John J. #WHOPS-002578]
with [KEY 12,C (General Access Shift 3 – Shift Supervisor Doe, John F. #WHMGR-02578)]
Log Date – July 4th, 2020, 22:36:28
[PALLET 00023 19243 23] was PLACED at [BIN 26 9 5]
by [LIFT 12] under Operator ID [Doe, John J. #WHOPS-002578]
with [KEY 12,C (General Access Shift 3 – Shift Supervisor Doe, John F. #WHMGR-02578)]
Log Date – July 4th, 2020, 22:50:41
[LIFT 12] ARRIVED in [MOTORPOOL SLOT 12]
under Operator ID [Doe, John J. #WHOPS-002578]
Unit SHUTDOWN and [KEY 12, C] REMOVED
Log Date – July 4th, 2020, 22:56:37
Operator ID [Doe, John J. #WHOPS-002578] successfully EXITS MOTORPOOL
Log Date – July 4th, 2020, 22:59:59
Operator ID [Doe, John J. #WHOPS-002578] [Key 12,C] RETURNS
to KEY HOLDER #12 [(General Access Shift 3 – Shift Supervisor Doe, John F. #WHMGR-02578)
Operator ID [Doe, John J. #WHOPS-002578] Clocks out
Operator ID [Doe, John J. #WHOPS-002578] Badges out of [Facility 2, A], San Antonio
———
End of Log
———
In this example, multiple tasks have been automated.
John J. Doe doesn’t lose productivity during any of the log data collection points. He only needs to carry out his job normally. The added data can be used to improve warehouse tracking accuracy as well. A warehouse automation system may also directly update shipping status inside of carrier applications and warehouse tracking software. Further warehouse automation benefits include:
Warehouse Automation Benefits
Businesses that automate their warehouses are currently outscaling the competition. They’ve found ways to break through the walls that are holding many warehousing operations back. They are reaping benefits such as:
Increased Productivity
Companies are taking advantage of the accuracy and precision of machines to manage repetitive tasks that can often result in injury for workers. These repetitive action injuries are common in more traditionally-operated warehouses, where cost and other factors prevent mechanical automation.
Improved Worker Satisfaction
Warehouse automation empowers businesses to assign and develop new roles for workers who will reskill from mundane tasks to working in more complex and satisfying roles. Many would prefer to practice programming, software engineering, sales, or another skill as opposed to lugging around boxes and scurrying to update logs due to lacking system integrations.
Open Database Connection (ODBC) connections allow businesses to access virtually any information stored with ShipWorks WMS software.
Increased Accuracy
Picking, product placement on the warehouse floor and shelves, and time efficiency are just a few examples wherein accuracy saves time. No misplaced inventory, no time spent driving a lift past unknown packages, and no time spent rearranging items on shelves or in bins culminates in hours saved per work week for most warehousing operations.
WMS systems are able to alleviate two of these three issues without mechanical intervention. Robots certainly can place cargo on shelves more accurately than people. They can also retrieve items from shelves with greater accuracy and less load-shift or container movement.
Having said that, software integration applies to multiple types of non-robotic hardware such as dimensioners, scales, printers, and scanners. Many hardware solutions such as these can be found in warehouses, so most warehouses can benefit from software-based automation immediately.
The bulk of profitability in warehousing and logistics automation, however, comes from eliminating systemic inefficiency, such as losing time to misplaced goods or poor warehouse layout.
Fewer Shipping Mistakes
When warehouses are more operationally efficient, consumers see the benefits immediately. Fewer misships, lost packages, and higher overall customer satisfaction. When customers receive the correct packages on-time over a long period, they build strong trust with their supply chain touchpoints.
Which Processes Can Be Automated in a Warehouse with ShipWorks?
Shipping
Shipping processes can be almost entirely automated using Shipworks software. Features such as rate shopping, rules-based shipping, and multi-warehouse shipping are all available to support business process optimization for warehouses. Shipworks even works with multiple dropshipping approaches to enable our customers to use whatever approach works best for them.
We offer additional benefits in the form of discounts on carrier-grade shipping insurance. We are commonly compared against carriers such as UPS, USPS, and DHL for shipping insurance.
Find out more about how you can save up to 74% on shipping insurance with ShipWorks.
Channels and Systems
When dealing with multiple sales channels and fragmented systems, businesses stand to lose substantial amounts of time to order processing efficiency. Shipping software supports ERP systems that may not otherwise process orders automatically. This benefit applies whether a business sells only on their ecommerce site or if they have chosen to include avenues such as selling directly on Amazon, AliExpress, Etsy, Ebay, or another set of sales channels altogether.
ODBC integrations ensure interoperability between legacy databases, third-party data sources, Exchange Data Interface (EDIs), ERPs, and even auxiliary data locations such as Private MySQL databases, privileged SQL servers, or even Google Sheets.
Order Importing
We use the term order to include any inbound order that comes from an Exchange Data Interface (EDI) from another company, including digitized purchase orders and orders placed through ecommerce or other online portals.
When your business must make the most of their available time, there’s no substitute for workflows that can be fully automated.
Operational Efficiency
Label printing, inventory planning and rotation, inventory analysis, and other tasks can be automated using ShipWorks. By combining the benefits of address verification with batch label printing, companies are able to shave tasks that can take hours per day down to take only a few minutes per day. Blue Sky Scrubs was just one of our clients who managed to save tens of thousands of dollars in labor per year using ShipWorks warehouse management solutions.
Security and Auditing
Information security is a priority for ShipWorks. We know what our customers stand to lose if user information is lost, stolen, deleted, or otherwise improperly accessed. We use a combination of account-based permissioning, user-level logs, and automated data backups to ensure your data and the data of your customers remains secure.
With ShipWorks You Get:
- Intelligent packing and fulfillment systems
- Automatically secure the best rates with Centralized smart rate shopping
- Multi-site optimization support—Including multiple online stores
- Rules-based shipping logic
- White-glove, real person support
- Bolster your pre-existing ERP or WMS without replacing it
- Intelligent Order Routing
- Exclusive discounts on carrier rates up to 62%
- Discounted, carrier-grade shipping insurance, on-demand
- Integrated accounting and analytics
- ODBC integration
- EDI, API support
- Dropshipping support
Conclusion
Compared with traditional warehouse shipping processes, ShipWorks saves both time and money while enabling our customers to scale their businesses, penalty-free.
Warehouse automation can unlock more than 2-3x gains in operational efficiency when implemented well. When you automate most of the traditional shipping tasks, you empower your warehouse to scale massively without adding to your headcount. Reach out for a demo or start a free trial now to learn more about how you can save, scale, and succeed at an unprecedented pace!