Guide to Growth: High-Volume Warehouse Hacks To Boost Efficiency, Minimize Costs, And Improve Order Fulfillment
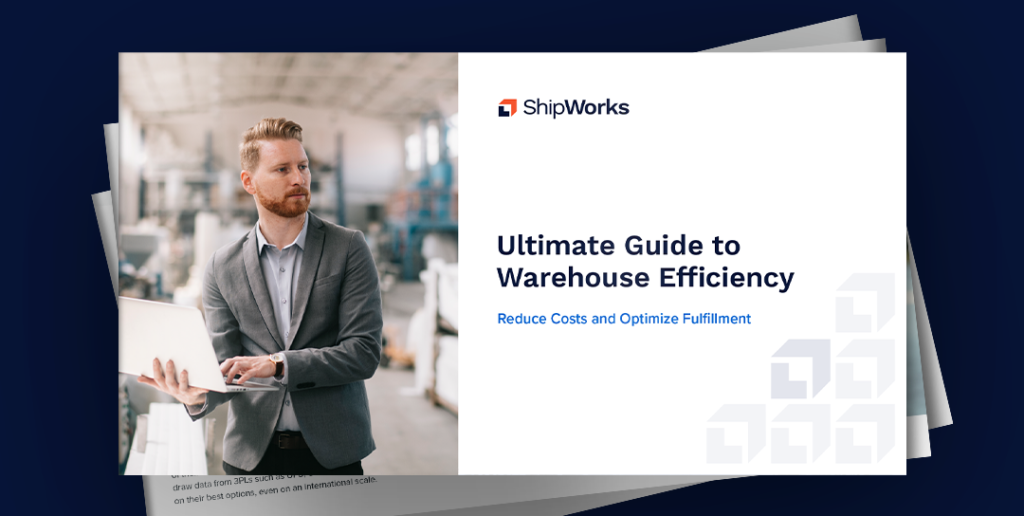
Warehousing is more important than ever. Supply chains are straining and some businesses are starving for resources. More than 40% of small business owners surveyed here stated that they are experiencing a rising cost of wages. Labor shocks contribute substantially to the currently rising costs of goods and services. Another substantial factor is the shortage of skilled truck drivers.
Truckers account for more than 70% of freight hauled in the United States. In May 2021, the American Trucking Association reported a need for more than 60,000 drivers nationwide to shore up demand. Increases in ecommerce and other forms of online business are beginning to show their additional strain on the supply chain. Walmart and Amazon are just two examples of eCommerce sources here.
These issues alone, however, do not comprise the sum of breaks in the modern supply chain. Third-party logistics (3PL) providers expect loads to be finished on time. Poor warehouse optimization can cause delays that, while short, cause further delays down the line. For example, a truck rolling into the distribution center five minutes ahead of schedule may leave six or seven minutes late if a load isn’t finished in time. Businesses turn to warehouse operations to prevent these sorts of avoidable delays.
Importance of Efficiency in Warehouse Ops and Logistics
Warehousing plays a vital role in logistics and delivery. Storing goods closer to the location they will need to be delivered minimizes the number of resources needed to set packages on customers’ doorsteps, in P.O boxes, and other locations. Companies that invest more heavily into operational efficiency often see higher customer satisfaction levels.
Further, efficient operations often lead to higher employee engagement and satisfaction. Some companies can take this to the “n-th” degree, but many businesses choose not to do so.
Operational automation often comes as a welcome change for businesses and employees alike. Less back-breaking work and more time to focus on fulfilling other business goals. One of the most common warehouse efficiency shortcomings is poor warehousing space optimization.
Understanding Common Warehouse Setup Mistakes
Poor warehouse space utilization costs companies more time and money every day. Whether slow-selling products are choking out space right by the shipping and fulfillment dock or high-demand products are stored two rows away from the dock, businesses are losing money. Many business owners are taking warehouse optimization far more seriously as they see their competitors flourishing by doing so.
Other serious warehouse set-up mistakes include:
- Lacking Inventory accuracy: When businesses aren’t precisely aware of their stock counts at each location, they run the risk of losing out on sales opportunities due to a shortage of supply. They also risk losing money to liquidate assets because products are positioned to close to bad markets and not close enough to capitalize on hot regions.
- Inventory Distribution Across Warehouses: Businesses may tend toward one form of inefficient inventory distribution or another. Two common forms include distributing inventory equally across all locations—foregoing market personalization—and sending products to whatever space is available.
- Failure to invest in warehouse management systems (WMS): Companies like Amazon and Walmart are using WMS to incredible effect. WMSs empower businesses to switch between picking methods, glean market-specific insights, and even optimize warehouse operations through RFID tracking and other means.
- Missed Opportunities to Automate: Automation provides four key benefits. Accuracy over human counterparts leads to fewer misships and returns. Speed advantages are numerous, perhaps most notable is the ability to fire and forget tasks such as bulk label printing. Systems that run without the potential to feel ill or call in sick offer reliability. Warehouse automation also assists with increasing overall warehouse efficiency without the ability to alter their programming, get tired, or otherwise introduce failure, which has the potential to generate immense efficiency.
Building a Resilient Supply Chain
Since COVID-19 came into the picture, it’s become glaringly clear that businesses must be ready for anything. Contributing to a resilient supply chain is key to ensuring continuity of operations. It is estimated that around 30% of US small businesses have shuttered since COVID rolled in.
Visibility, integration, and automation are the three most important factors in modern warehouse efficiency. Businesses must be able to see what resources they have in which locations, where they need to allocate more resources, and how they can further improve their bottom line. Automation has a clear line to the bottom line—fewer worked hours. Visibility, however, is often harder to evaluate. Siloed data, such as information stored within isolated warehouse systems can hamstring efforts to plan inventory location on a national or international basis.
One of the best ways to drive higher warehousing efficiency is through warehouse management and shipping software that allows businesses to automate multiple functions in one location—particularly so when they can integrate several warehouse systems through Open DataBase Connection (OBDC) or other means.
Among the most ideal situations for entrepreneurs are plug-and-play (PnP) systems. These allow businesses to integrate systems directly into their business, without causing vendor-specific issues or other barriers that slow operations down.
Get Started
See how ShipWorks can help optimize your fulfillment workflow and scale as you grow.